
Indirect costs also include rent, insurance, depreciation, and quality control.
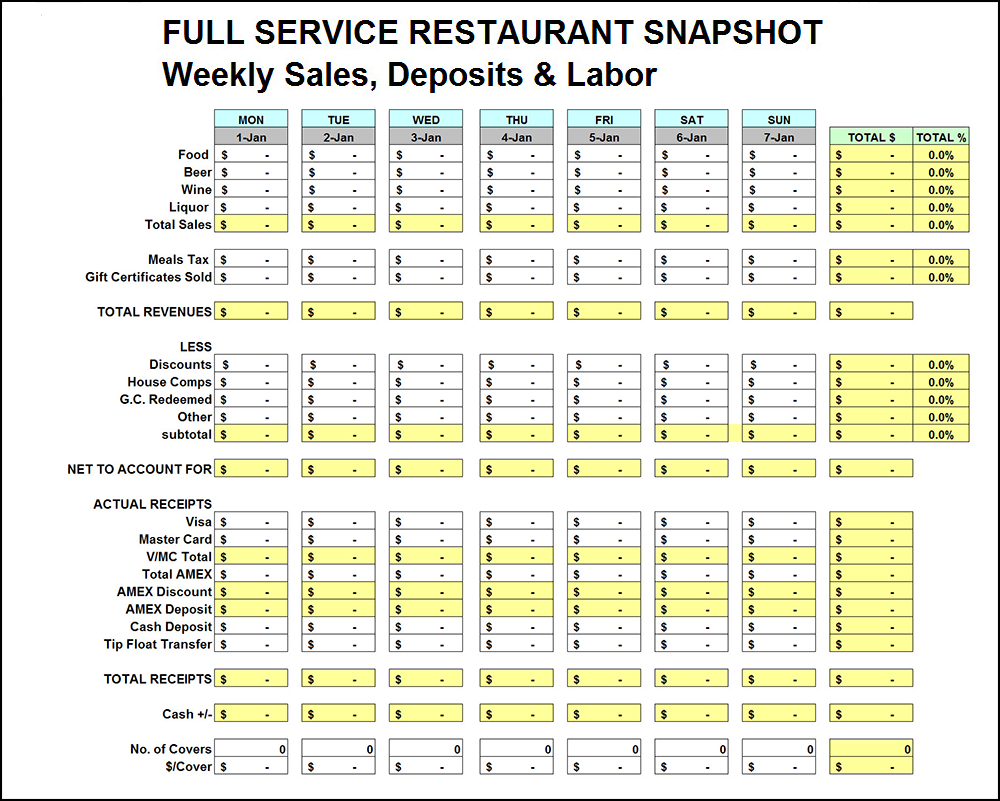

Indirect labor contributes to your company’s overhead, but these costs aren’t attributed to a particular product or service because the roles relate to the entire business. The salaries of payroll staff, sales team members, administrative assistants, and office managers are labor costs that are considered indirect. Administrative expenses are a common example. Indirect labor costs include costs that are not linkable to a specific product or service that your business offers consumers. In manufacturing, the salaries of your engineers, production supervisors, truck drivers, and assembly line workers are considered direct labor costs. If an employee uses raw materials or tools to develop your business’s product or service, their salary is a direct labor cost example. Direct costsĭirect expenses are the costs associated with a specific object, such as raw material, software, or tool used the create your company’s product or service. There’s a significant difference between direct and indirect labor costs, and you should consider both when measuring labor costs’ impact on your business. What’s the difference between direct and indirect costs?

In small-medium businesses especially, labor costs can make up a large percentage of your overall costs. Overtime, sick pay, maternity pay, and training costs all contribute, so your total labor cost will be much more than just employees’ basic salaries.
Labor hour calculator plus#
The total amount includes the salaries for hourly and salaried workers, plus employee taxes, bonuses, and company-specific extras such as employee compensation schemes. In short, labor cost in manufacturing industry is the total amount spent on employees by your company.
